Component Cleanliness Testing for Liquid Systems
Contamination from fluid handling components can eventually reach the processing environment either in the form of solid particulates or, through chemical reaction, as a form of ionic contamination. Due to the cost associated with any yield impacts, components must be ensured clean prior to their use in production equipment, which will interact with the final product. Establishing a simple component test program that will confirm initial and long-term cleanliness of critical fluid handling components down to 20 nm for plastic contaminants and < 9 nm for metallic contaminates using Particle Measuring Systems Ultra DI® 20 or Chem 20™ liquid particle counter is discussed here. This simple step can save both time and money in the production environment by selecting the best components for the designated task.
In liquid handling systems components such as valves, pumps, filters, degas modules, etc. are common sources of particles.
A simple test station can be constructed to help determine which component type and supplier has the lowest particle shedding or generation (see full paper for test schematic). This test setup can also be used to determine component- to-component variability. It is an easy set up that can be established by the component manufacturer or component user.
The setup includes a bypass line around the component under test to allow continuous flushing when the test piece is removed, thereby maintaining system cleanliness at all times. It is recommended that after every new component under test is installed or removed, water is flushed through the system to remove any air in the lines before the particle counter is turned on.
Topics discussed in this paper:
- Fluid systems and their sources of contamination
- Valve, pump, filter and degas module testing
- Recommendations for fluid system setups to reduce contamination
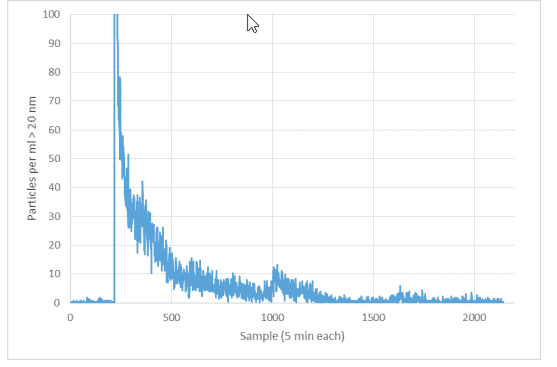