FORCE & HARDNESS
For force measurement, the process of calibration is the comparison of applied forces indicated by a measurement system under test to a calibration standard. The traceability of the standard used defines the resulting range and accuracy of the system being tested
Hardness Calibration should be performed on a periodic basis to verify that the accuracy of the instrument is within the manufacturer’s stated tolerances for the grade or model. As a hardness tester repeatedly measures the relative resistance of materials to denting, bending, or scratching, it can become misaligned. Calibration and adjustment will be required to restore its reliability.
STANDARD UNITS
FORCE GAUGES
Digital force gauge is force measuring device which has load cell inside. Digital force gauge indicates the measurement digitally, which reduces the human reading errors of test results and enhance the repeatability.
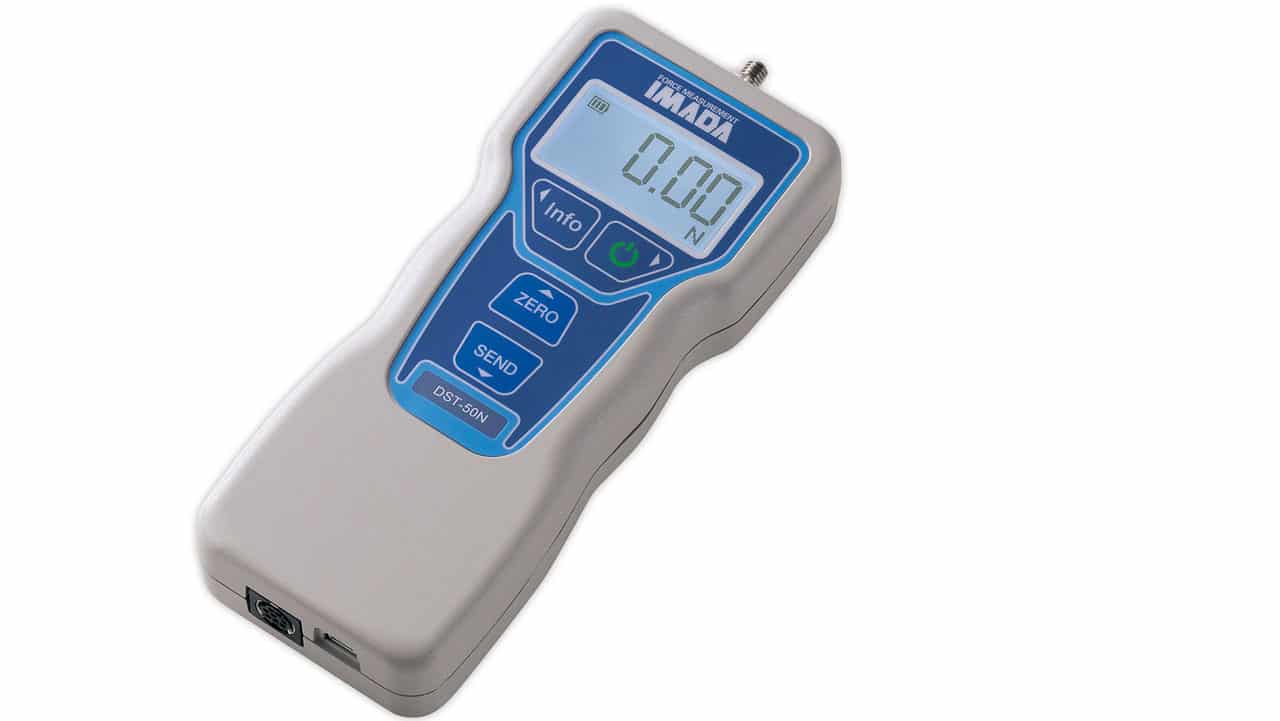
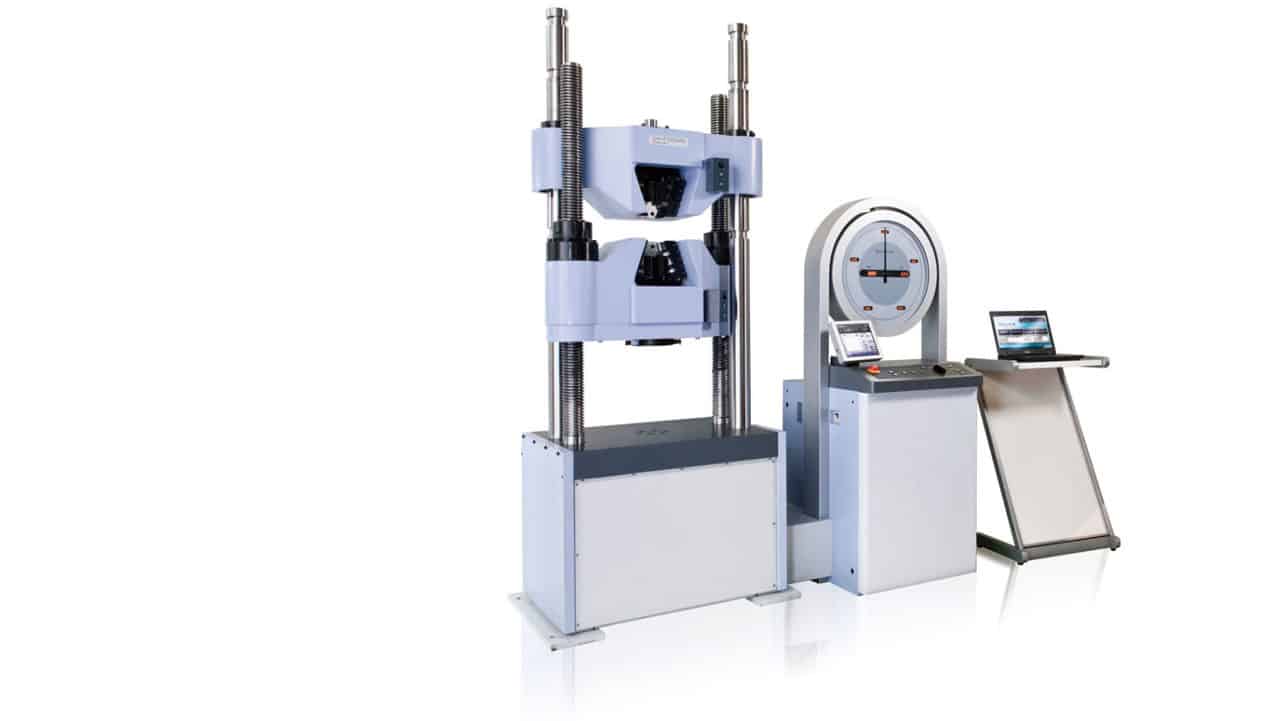
TENSION AND COMPRESSION
Tension and compression refer to forces that attempt to deform an object. The main difference between tension and compression is that tension refers to forces that attempt to elongate a body, whereas compression refers to forces that attempt to shorten the body.
TENSION METER
These tension gauges are used as handheld devices and sensors for the continuous tension measurement with one or three rollers, whereby sensors with one roller can replace an existing deviating point.
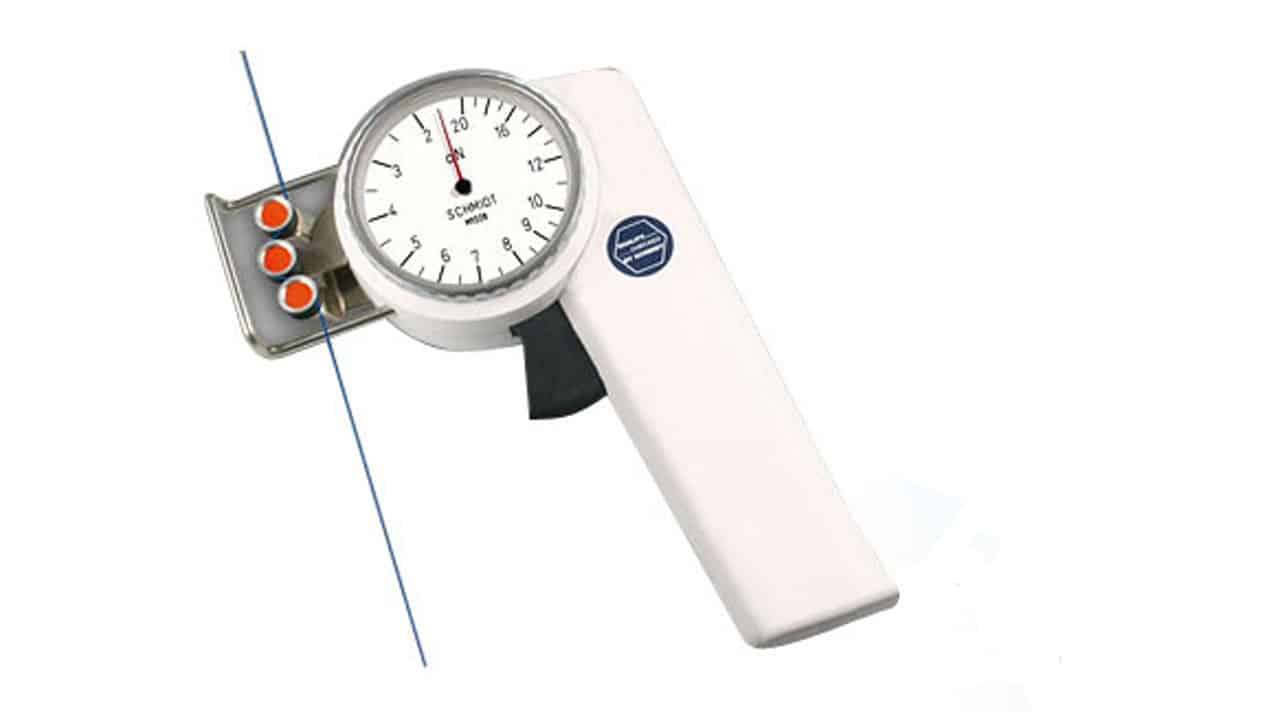
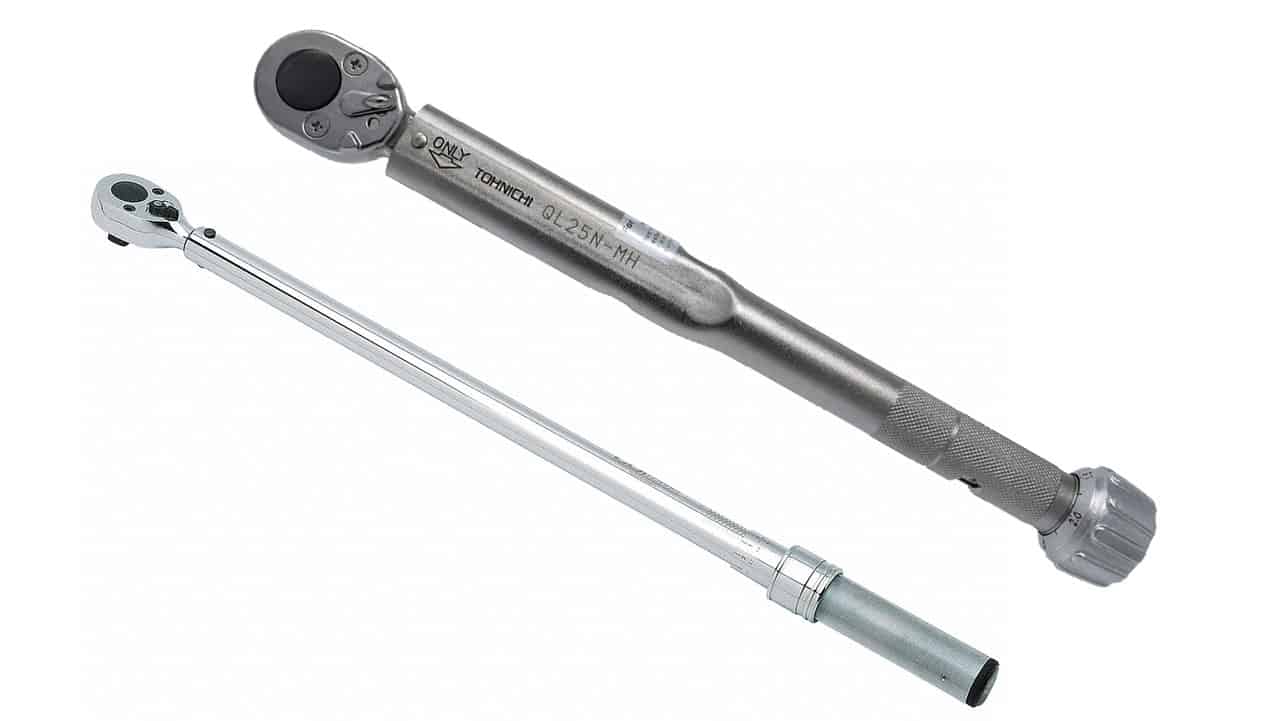
TORQUE
In physics and mechanics, torque is the rotational equivalent of linear force.[1] It is also referred to as the moment, moment of force, rotational force or turning effect, depending on the field of study.
DIGITAL TORQUE METER
The torque meter consists of a hand-held measuring device and an external torque transducer. The torque wrench tester is delivered adjusted
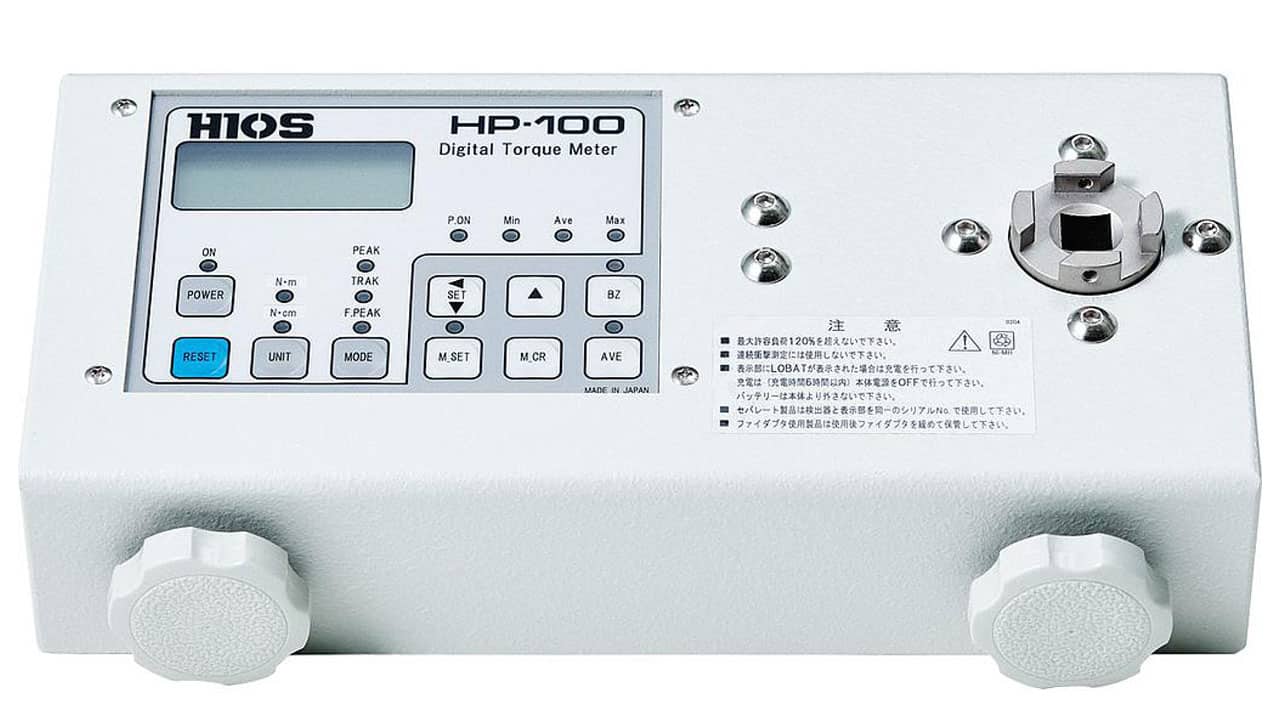
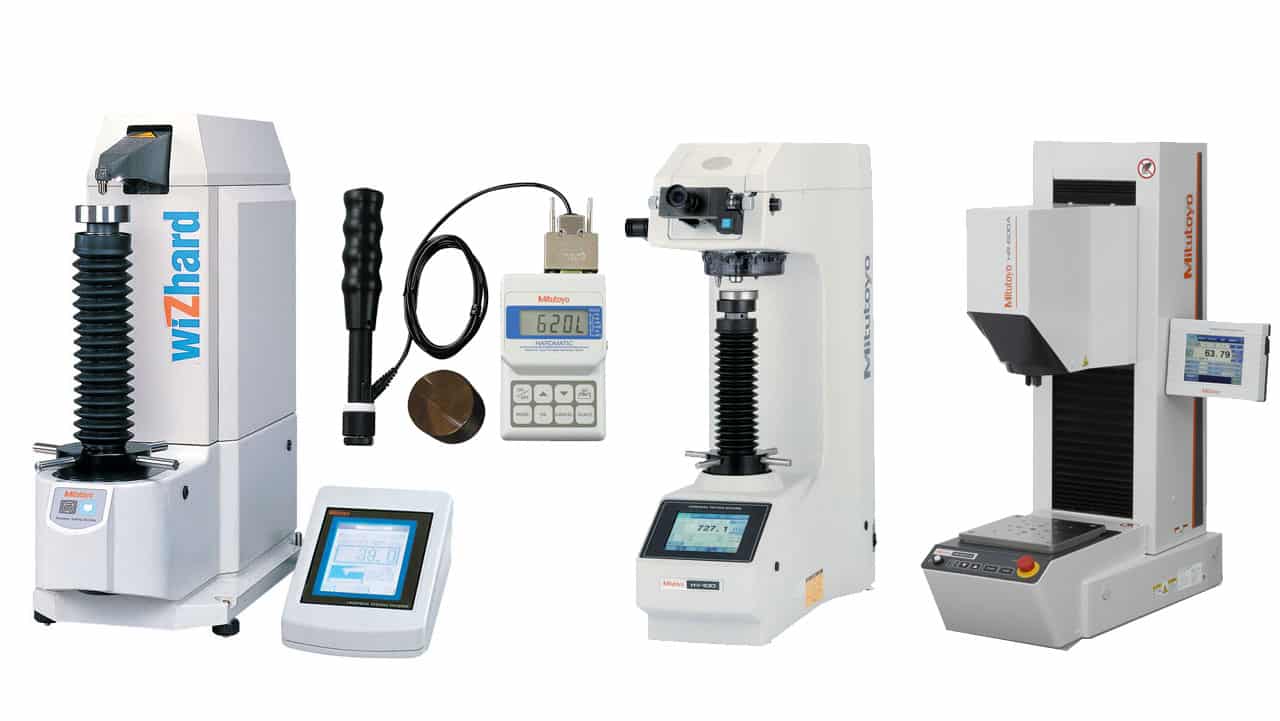
HARDNESS TESTER
Brinell Hardness Test
The first widely used standardized hardness test, the Brinell method determines the indentation hardness of metal materials and is typically used for materials with a coarse surface or a surface too rough to be tested through other methods.
The Brinell test is not useful for fully hardened steel or other hard materials, however, and often leaves a large impression on the metal. The Brinell test is also very slow.
The first widely used standardized hardness test, the Brinell method determines the indentation hardness of metal materials and is typically used for materials with a coarse surface or a surface too rough to be tested through other methods.
The Brinell test is not useful for fully hardened steel or other hard materials, however, and often leaves a large impression on the metal. The Brinell test is also very slow.
Rockwell Hardness Test
Developed to provide a less destructive alternative to the Brinell test, this differential-depth method eliminates the errors associated with mechanical imperfections.
Quicker and cheaper than the Brinell and Vickers tests, the Rockwell test requires no material prep, and hardness value is easily readable without any extra equipment, making this one of the most commonly used methods of measuring metal hardness.
Developed to provide a less destructive alternative to the Brinell test, this differential-depth method eliminates the errors associated with mechanical imperfections.
Quicker and cheaper than the Brinell and Vickers tests, the Rockwell test requires no material prep, and hardness value is easily readable without any extra equipment, making this one of the most commonly used methods of measuring metal hardness.
Vickers Hardness Test
Making use of a diamond indenter, the Vickers hardness test is done with less force and more accuracy than the Brinell test. By magnifying the surface of a metal, this test can target specific microstructural constituents like martensite or bainite, or assess the quality of heat treating or surface hardening operations.
Requiring an optical system and material prep, the Vickers test incurs higher costs and takes longer to complete than the Rockwell test.
Making use of a diamond indenter, the Vickers hardness test is done with less force and more accuracy than the Brinell test. By magnifying the surface of a metal, this test can target specific microstructural constituents like martensite or bainite, or assess the quality of heat treating or surface hardening operations.
Requiring an optical system and material prep, the Vickers test incurs higher costs and takes longer to complete than the Rockwell test.
HARDNESS TEST BLOCKS
a comprehensive range of hardness reference materials (hardness test blocks) to suit your quality management procedure perfectly.
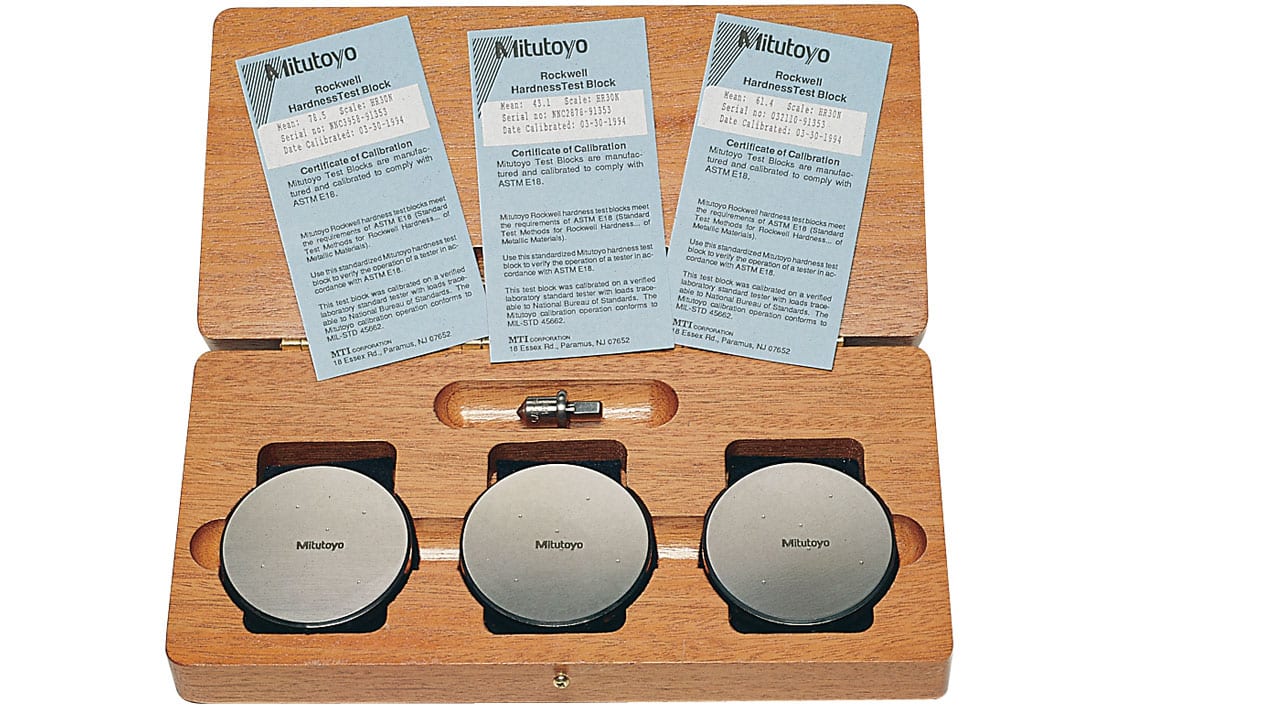