Recent Advances in Regulatory Compliance with Pharmaceutical Viable Air Monitoring in ISO 5 – 8
An ISO 7 cleanroom is the final area where microorganisms are tolerated. Within this area, there should be strong measures to avoid any contamination build-up. Data from this environment is essential for troubleshooting and understanding the microflora of the clean zone concept. For efficient setup of critical control points, recording and traceability of sampling data is key for keeping the room under control. Before classifying ISO 7 and ISO 5 areas, manufacturers should understand the critical control points within these rooms. Mapping is a very inefficient process, with long periods of waiting on the outcome of impaction sampler results. Usage of real-time monitoring equipment that provides immediate responses to the room when “at rest” and “in operation” expedites the mapping process.
In a classification scenario, sampling 1 m³ air is mandatory. Monitoring these rooms for a prolonged sampling time is associated with a lower flow rate and will give more information than sampling for a 10 min “snapshot”. Therefore, 25 or 50 LPM instruments that provide a sampling volume of 1 m³ within a respective 20 min or 40 min timeframe are preferable and are better monitoring practice.
Download this article for a discussion on how ISO 7 and 8 areas protect the aseptic core of manufacturing suites, in addition to non-classified areas. For a successful cleanroom, all contamination brought into these supporting areas must be removed and prevented from proceeding into higher-level areas.
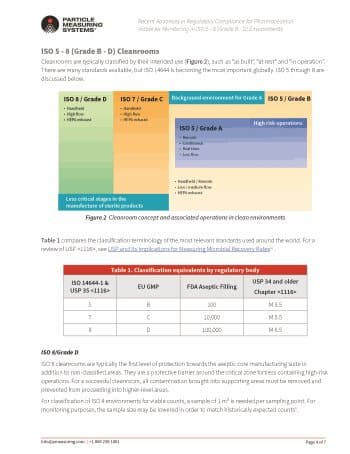