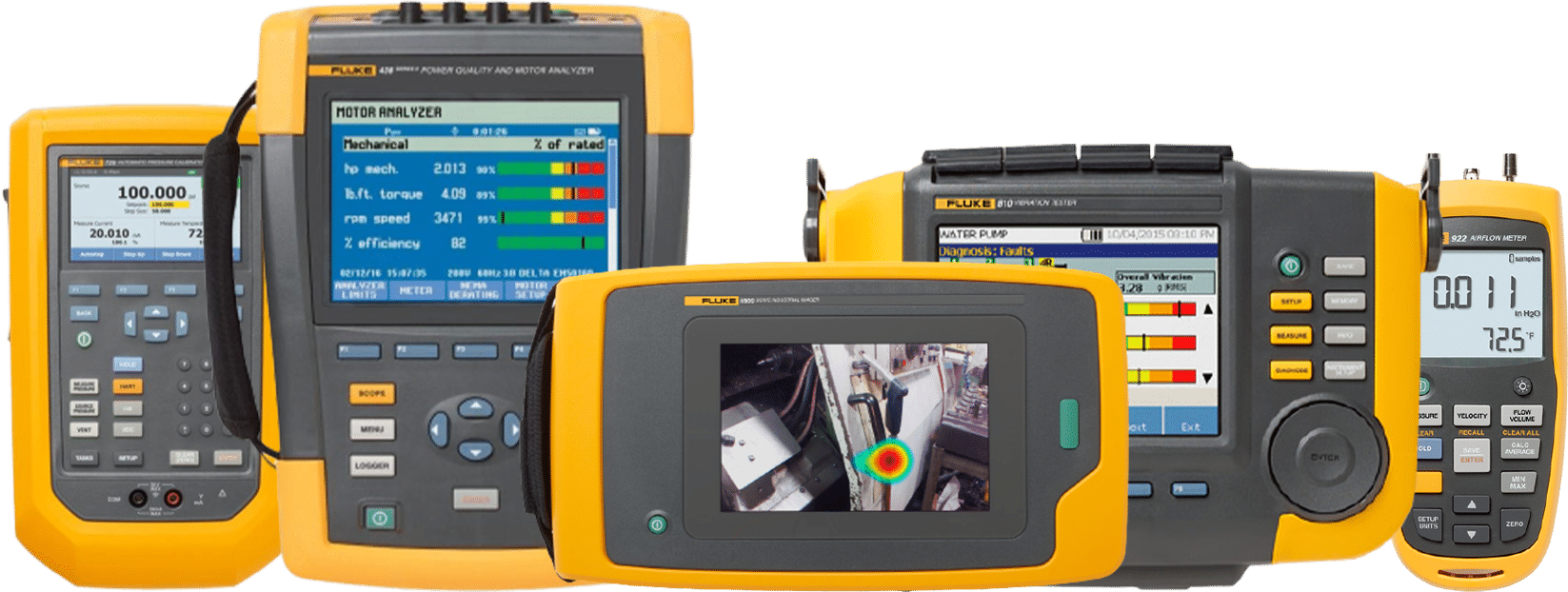
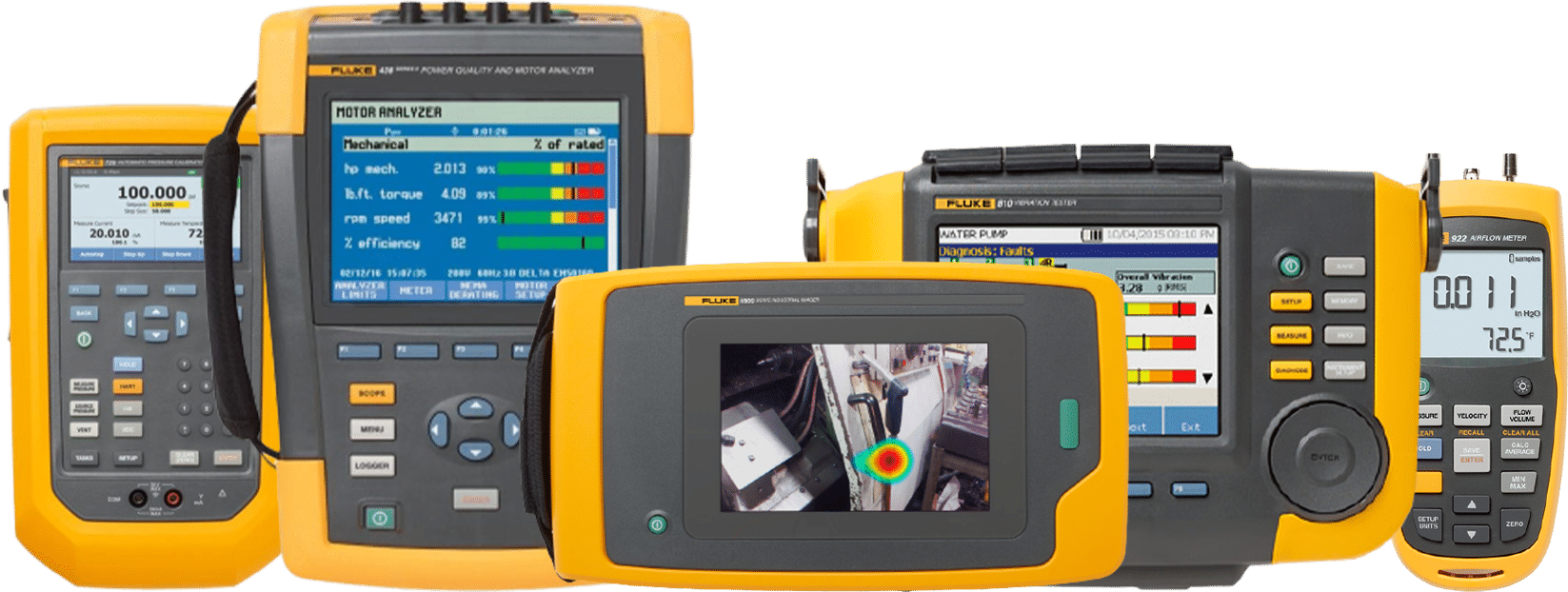
Select a topic to get started
4 proven solutions to optimize production process
1. Don’t underestimate the consequences of compressed air leaks
Although invisible, compressed air/gas leaks can affect product quality, production process and cause safety issues.

Leverage on Fluke’s breakthrough acoustic imaging technology to quickly & accurately pinpoint compressed air, vacuum, gas or steam leaks.
- Ultrasonic leak detection up to 52/100kHz
- Locate leaks up to 70/120m
- Save up to 75% of your inspection time
Report leaks by pictures.
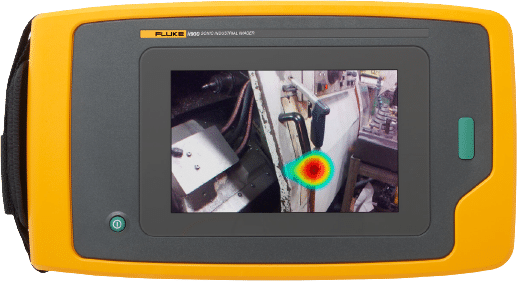
2. Detect electrical & mechanical stresses that are damaging your motor without stopping the machine
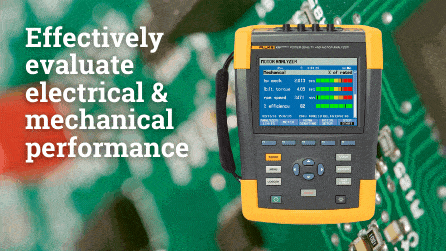
Effectively evaluate electrical and mechanical performance just by hooking up voltage and measuring current, providing you with an unprecedented level of data.
- Calculates motor efficiency without mechanical sensors
- Full power quality and electrical energy analyzer functionality
- Automatically calculate motor derating according to NEMA/IEC guidelines
Add motor analysis to your maintenance routine.
- Poor power quality has a direct correlation with motor performance
- Find out the impact of torque on overall performance and efficiency
- Motor efficiency has a direct impact on the bottom line
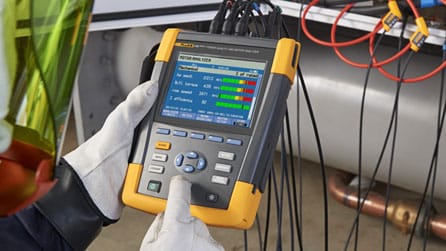
3. Enhance process control system to drive lean production
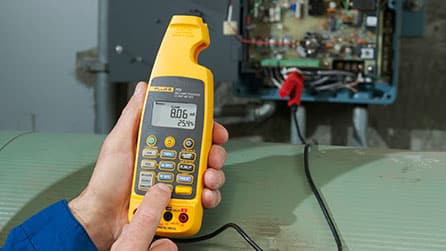
Troubleshooting can easily take up 80% of a technician’s time. Overcome this challenge without the need to stop operation.
- Measure 4-20 mA live control signal without breaking a loop
- Get all the instrumentation troubleshooting and verification needs in just one tool
- Resolve signal issues for PLC and control system analog I/O
Save significant time from making multiple routine trips.
- Do more for less by covering various tasks in pressure, temperature, electrical loop etc.
- Accurately identify errors and correct it with HART protocol
- Integrated workflow for a complete field calibration process that automates and documents the test results
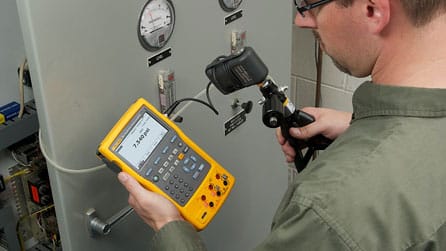
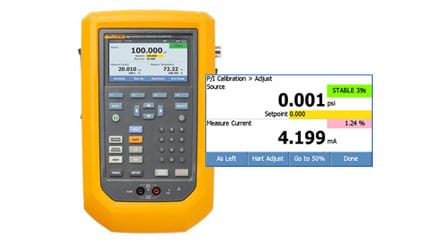
Simplify and increase quality results for pressure testing
- Up to 1000 psi automated pressure calibration run in the field or lab
- Speeds up calibration process while overcoming common pressure testing instability and repeatability challenges
- Significant time-saving with built-in test templates to speed up test procedures and save test results
4. Proper indoor air quality to regulate building health and manage energy costs
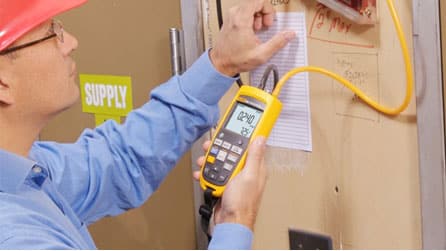
Contaminants control via pressure differential between clean room and external environment.
- Diagnosing ventilation issues down to 0.001 in H2O resolution level
- Ensure proper air pressure, air velocity, and cfm air flows
- Perform duct traversals for HVAC maintenance
Conducting airborne particle control.
- Verify industrial cleanrooms by capturing airborne particle concentrations
- Measure filter efficiency
- Load studies for production line expansion
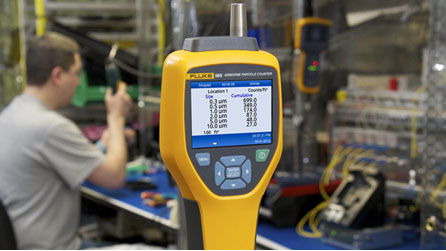
Select topic to learn more
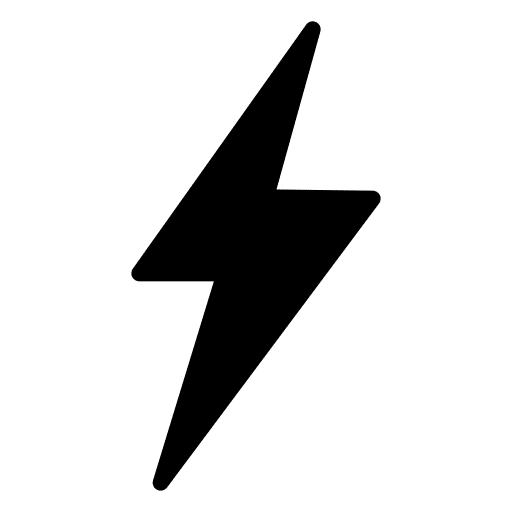
Energy management
4 proven solutions to identify energy wastages
1. Prevent motor mechanical waste
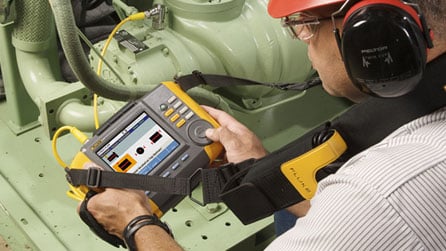
Get immediate answers to mechanical issues with Fluke 810 Vibration Tester.
- Powerful diagnostic results covering not just the problem but also the location and repair recommendation
- Identify root causes to prevent unplanned downtime
- Tri-axial accelerometer sensors reduces 2/3 of the measurement time than using single axis sensor
2. Do regular checks on HVAC systems
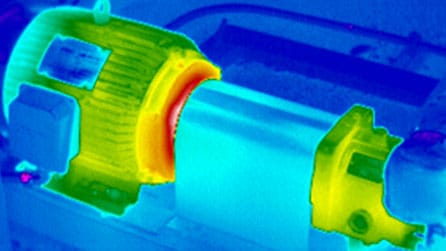
Early detection of system issues and inefficiencies can be easily done with thermal solution.
- Prevent system damage by detecting heat emissions from mechanical components
- Improve energy and operational efficiency
- Inspect pipeline blockage, water leakage, or other building diagnostic issues
In HVAC process, variations in thermal pattern detected in thermal images could indicate corrosion, leaks or blockages.
Conduct inspections (mechanical/electrical/buildings) and discover the potential root causes for abnormal thermal patterns.
- Noncontact measurement
- Little or no interruption to operations
- Reduce costly downtime and equipment damage
Shoot images near or far, with thermal imagers equipped with high infrared resolution up to 680×480.
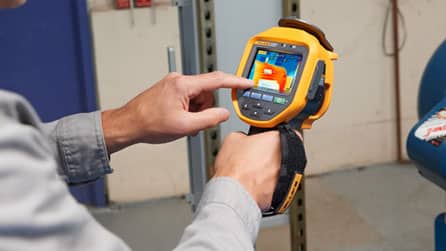
3. Minimize waste in electrical system
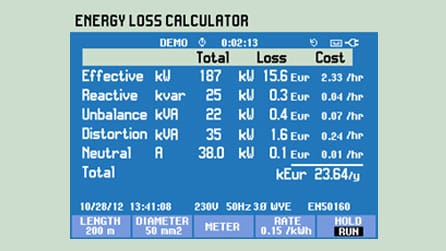
Quantify, pinpoint and know exactly how to recover energy losses.
- Effective: Amount of energy dissipated as heat when current flows through cable
- Reactive: Energy loss as a result of inductive and/or capacitive loads
- Unbalance: Loss in energy due to an unbalance distribution in source and load
- Distortion: Amount of energy lost as a result of distorted power (harmonics)
- Neutral: Energy loss due to currents in a neutral conductor
Breakthrough technology to measure motor performance while the motor is operating inside the machine.
- Use an innovative algorithm to calculate motor output torque, power, speed and efficiency based on the input three-phase electrical power, without the need to install mechanical sensors
- Analyze motor load condition according to NEMA limits
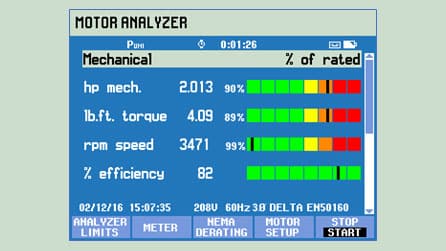
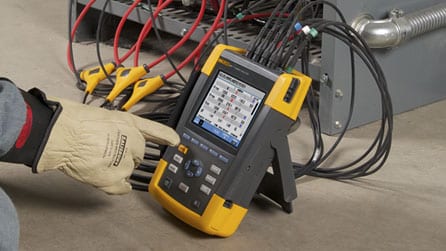
Key Features:
- Quantify energy wastage in your power system for effective identify utilities saving
- Efficiently detect root causes of power quality issues
- Understand energy saving ROI and prioritize tasks with unified power function for optimum power loss analysis and onboard power loss calculation
- Independently verified IEC61000-4-30 Class-A standards compliant portable analyzer to deliver consistent and accurate measurements
4. Recover compressed air or gas wastages
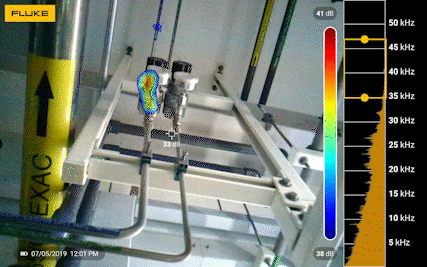
See compressed air and gas leaks in CVD and dry etching.
- 75% time-savings compared to conventional leak detection methods
- Multiple leak sources can be seen within the display
- Color display with rich data for easy visualization during indoor or outdoor use
Ensure safety and prevent further air/gas wastes.
- Highly sensitive acoustic technology: detects as far as up to 120 metres
- Image or video capturing modes available
- Share leak rate and cost estimation with Leak scale and LeakQ reports
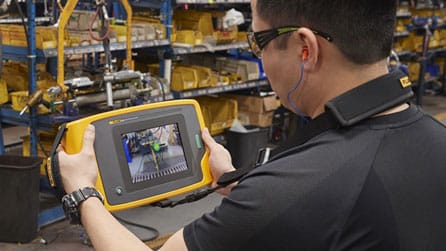