Understanding ISO 14644-2:2015 Cleanroom Monitoring
After the recent release of the ISO 14644-1:2015 Revision Summary and Understanding ISO 21501-4 application notes, Particle Measuring Systems (PMS) continues the ISO Standards interpretation series of documents with the evaluation of the newly released ISO 14644-2:2015.
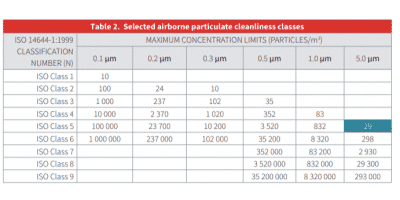
This document underlines the major changes between the previous version of ISO 14644-2 and the latest, second edition, dated December, 12th 2015.
A specific approach to the best practices to be adopted for an efficient and compliant cleanroom monitoring process are discussed.
In combination with the revision to Part 1. Classification of air cleanliness by particle concentration of ISO 14644-1:2015, the ISO Technical Committee TC 209 has been working on the update to the basic airborne cleanliness monitoring guidelines contained in ISO 14644-2.
The TC 209 community voted in favor of the revision to update and improve the standard specifically to:
- Simplify and clarify requirements and guidance tables that specify frequency of testing and monitoring of cleanrooms used to demonstrate continued compliance with the cleanliness classification
- Refine how these intervals may be extended, provided that automated monitoring systems show the cleanroom is under control
- Provide new guidance on aspects that should be considered when configuring a monitoring system for a cleanroom
The new standard’s introduction also lists the goals of the ISO 14644-2, when successfully applied:
- Emphasize the needs and advantages of a planned cleanroom contamination monitoring
- Provides the method for a correct particles contamination alarm and warning limits setting, based on a careful evaluation of data trends
- Define the differences between a simple periodic cleanroom control and a more intensive/complex monitoring strategy
- Enhance the installation and process knowledge, as to improve the risk assessment evaluation and a faster reaction to any unexpected cleanroom performance
- Concretely reduce the operation cost by preventing production loss